產(chǎn)品中心
化學鎳鍍液NSB-1M/A/D
NSB-1為一弱酸性鎳/磷合金化學鎳鍍液,鍍層中的磷含量較高,耐蝕能力強,適合于印刷電路板之細線路的表面處理,對綠漆及干膜之攻擊性低,與硬板及軟板之兼容性佳,具有穩(wěn)定磷含量及浴安定性。
在線咨詢
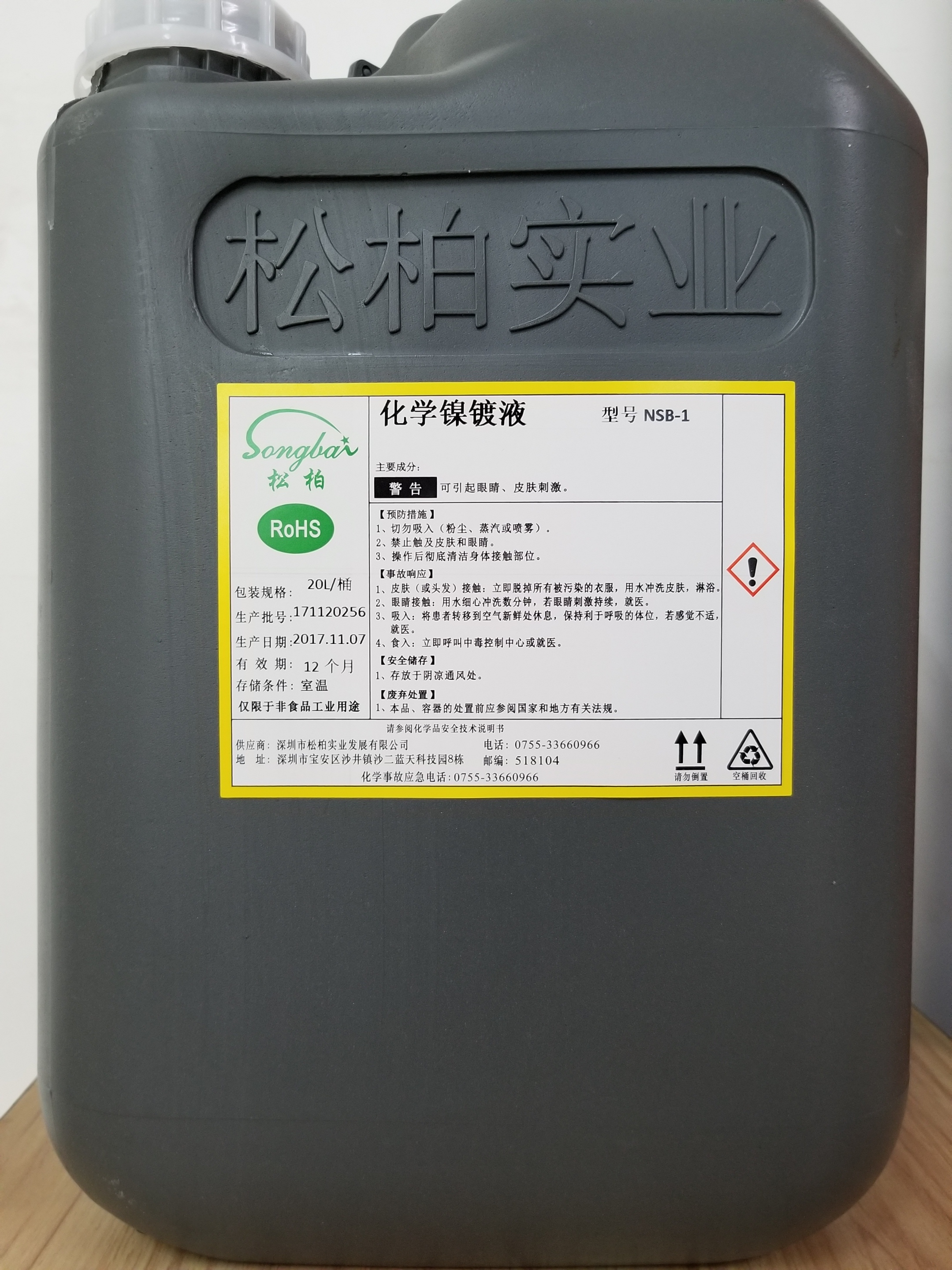
特性
應用
技術(shù)指標
備注信息
- 鍍液特性:
Ni = 90 ± 2%(重量百分率)
P = 10 ± 2%(重量百分率)
在84℃條件下,NSB-1藥水的鎳層析出速度為6-9μinch/min
- 藥液組成:
主成分 | 性狀 | |
NSB-1M 建浴用 | 還原劑,錯合劑,添加劑 | 無色透明 |
NSB-1A 建浴、補充 | Ni 鹽 | 綠色透明 |
NSb-1D 補充用 | 還原劑,錯合劑,添加劑 | 無色透明 |
建浴或添加藥水時請穿戴橡膠手套及安全眼鏡,小心操作。
- 設備:
加熱 使用不銹鋼(#316)材質(zhì)、石英或Teflon包覆之加熱器,須防止局部過熱
及設置溫度自動控制器
過濾 使用5-20μm P.P. 濾心,連續(xù)過濾,循環(huán)量3-7 cycle turn/hr
擺動 擺動(rock)速度約0.3-0.6 m/min
震動 需有氣壓缸震動,沖程約4-6cm 頻率為每5-10秒ㄧ次
- NSB-1使用方法:
- 加入浴量1/2的純水
- 加入110ml/L的NSB-1M 并持續(xù)攪拌
- 加入59ml/L 的NSB-1A 并持續(xù)攪拌
- 使用氨水調(diào)整至所需的pH值,再加純水調(diào)整液位,加溫至操作溫度,并持續(xù)攪拌
使用條件:
標準 | 范圍 | |
浴溫 | 84℃ | 83℃~85℃ |
浴負載 | 0.5 dm2/L | 0.3~1.0 dm2/L |
Ni濃度 | 5.9 g/L | 5.8~6.0 g/L |
pH(建浴時) | 4.85 | 4.8~5.0 |
循環(huán)量 | 5 cycle/hr | 3~7 cycle/hr |
擺動速度 | 0.5 m/min | 0.3~0.6 m/min |
Ni濃度及pH 管理條件:
Ni濃度管理
建 浴 時 | 5.9g/L |
連續(xù)使用中設定 | -0.1g/L ~ +0.1g/L |
NSB-1A 10mL
NSB-1D 9mL
(9%)氨水 9ml
補充方法:
- 可由自動分析添加系統(tǒng)或板面積之方式添加
- 每次補充以0.05g/L為補充一次量(最大補充量以不超過0.1g/L為限),避免因補充量過大而造成反應活性不足而停止反應
調(diào)高pH:以9%氨水調(diào)整。
調(diào)低pH:以10%H2SO4溶液調(diào)整。
補充方法:
- 在生產(chǎn)過程中分析鎳濃度的消耗而補充 3 種不同成份的藥液(A、B、9%氨水)。各MTO 毎相當于 1gNi 的補充量
MTO | pH | NSB-1A | NSB-1D | 約9%氨水 |
0~4.0 | 4.85 | 10mL/L | 9.0mL/L | 9mL/L |
- 配槽時按建浴方法開缸后,再利用9%氨水或10%硫酸(A.R.級)調(diào)整pH至標準值。
- 將補充液加在充分攪拌的區(qū)域,可使鍍液更加安定。
- 若鎳濃度比設定值降低0.5g/L以上,若一次補充(5 ml NSB-1A /每公升槽液)時,將產(chǎn)生覆蓋性不良的情形,也可能使反應停止:建議Ni2+濃度比設定值降低0.1g/L時,立即補充。
- 補充前請勿將A劑和氨水混合.如有因帶出及移槽時鍍液的流失量較多的情形。必須使用建浴劑(M&A劑)補充。
- 干膜溶出物會抑制析出速度,會有肩薄現(xiàn)象發(fā)生,請適時使用活性碳處理鍍液。
- 藥液分析方法:
準備藥品:
濃氨水(28%)
MX 指示劑
0.05 M EDTA 標準液
分析程序:
- 正確吸取鍍渡5mL于350 mL錐形瓶
- 加純水約100mL
- 加入氨水(28%)10mL
- 加入約0.4g MX指示劑
- 用0.05 M EDTA滴定
- 終點:由棕色變紅紫色
Ni濃度(g/L)=V(EDTA)×0.587×F
F:0.05 M EDTA標準液的標定系數(shù)
NSB-1鍍液中次磷酸二氫鈉分析
準備藥品及器具:
0.1N I2
250ml磨砂錐形瓶
0.1N Na2S2O3
25ml吸管
6N HCl
2ml吸管
分析程序 :
- 取槽液2ml放進250ml磨砂錐形瓶內(nèi)。
- 加入20ml 0.1N I2溶液。
- 取25ml 6N HCl沿瓶壁洗下殘留的藥液后,蓋上瓶蓋,置于暗室一小時。
- 另做一空白試驗重復.2-.3。
- 加入淀粉指示劑,以0.1N Na2S2O3滴定之。
- 終點:由紫色變無色。
SHP (g/L)=(空白滴定ml數(shù)-SAMPLE滴定ml數(shù))x 2.6
NSB-1之次磷酸二氫鈉控制在 25-36g/L
*生產(chǎn)中非因NSB-1系列藥水濃度不足或藥水本身成份異常,所造成的報廢,皆不在本公司賠償之范圍內(nèi).
- 化學鎳NSB-1問題與對策:
問 題 | 原 因 | 對 策 |
鎳與銅鍍層密著不良 | 1)綠漆殘渣附著于銅面 | a)顯影后,用H2O2-H2SO4處理 b)確認及加強前處理制程與清潔劑 |
2)顯影液中的界面活性劑殘留 | a)顯影后,用H2O2-H2SO4或SPS- H2SO4處理 b)確認及加強前處理制程與清潔劑 |
|
3)鍍鎳時綠漆溶出 | a)更新鍍液 b)確認綠漆特性(類型),硬化條件及 前處理流程 |
|
4)銅面前處理不良 | a)確認及加強前處理流程(刷磨、清潔劑、微蝕等) | |
5)水洗不良 | a)更換水洗水,加強擺動 b)確認及增加水洗槽進水量 |
|
6)活化后水洗時間過長 | a)縮短至2分鐘以內(nèi) b)增加水洗槽進水量 |
|
7)金屬/有機雜質(zhì)混入Ni 鍍液中 | a)更新鍍液 b)確認雜質(zhì)來源 |
|
金與鎳鍍層密著不良 | 1)金屬(尤其是Cu)或有機雜質(zhì) (綠漆等)混入Au鍍液中 |
a)更新鍍液 b)確認雜來源 |
2)Ni鍍層表面氧化 | a)更換水洗水 b)減少移位時間/加強鍍鎳后水洗 |
|
3)Ni槽有機污染(綠漆等) | a)更新鍍液 b)確認雜來源 |
|
露銅 | 1)Ni槽補充不適當 | a)由手動分析Ni/pH并做調(diào)整 b)檢查及調(diào)整控制器/補充裝置 |
2)銅面前處理不適當 | a)檢討前制程及銅面前處理 b)確認及加強前處理 |
|
3)鍍Ni液pH太低 | a)用氨水調(diào)整pH值 b)檢查及調(diào)整控制器/補充裝置 |
|
4)Ni液溫度太低 | a)調(diào)整至正確操作溫度 | |
露銅 | 5)活化不足 | a)檢查及調(diào)整鈀/硫酸濃度 b)更改活化處理基準 |
6)活化后水洗時間太久 | a)縮短水洗時間 | |
架橋 | 1)活化液污染(尤其是Fe,Cl) | a)檢查污染來源 b)預浸及活化槽使用高純度硫酸 |
2)活化液老化 | a)活化液更新 b)確認活化液的加熱方式,循環(huán)過濾及使用稀硫酸添加等 |
|
3)Ni槽補充異常 | a)手動分析Ni/pH并做調(diào)整 b)檢查補充量 c)檢查及調(diào)整控制與補充裝置 |
|
4)Ni槽液溫度太高 | a)調(diào)整至正常操作溫度 | |
5)刷壓過大 | a) 檢查及調(diào)整刷壓 | |
跳鍍 | 1)Ni槽補充異常 | a)檢查補充量 |
2)Ni 槽攪拌太強 | a)調(diào)整至最佳攪拌速率 | |
3)Ni 槽金屬雜質(zhì)污染 | a)確認污染源 | |
4)綠漆溶入鍍液中 | a)更新鍍液 b)確認清潔劑,綠漆特性及硬化條件 |
|
鍍層表面粗糙 | 1)Ni 鍍液pH太高 | a)用硫酸調(diào)整pH值 b)檢查及調(diào)整控制器/補充裝置 |
2)錯合劑太低 | a)補充建浴劑 | |
3)Ni 鍍液中有不溶性顆粒 | a)加強過濾 b)保持連續(xù)循環(huán)過濾 |
|
4)前處理不良 | a)改善前處理流程(微蝕)或清潔劑 | |
5)不溶性顆粒帶入Ni鍍液中 | a)加強過濾 b)更新鍍液 c)確認水洗槽流量,水洗時間及水 洗stage |
|
6)水質(zhì)不潔 | a)移槽過濾,加強過濾 b)配槽及補充液位都使用純水 c)更新鍍液 |
|
針孔 | 1)Ni鍍液中有不溶性顆粒 | a)移槽過濾,加強過濾 b)確認過濾條件(循環(huán)速率濾材孔 徑) |
2)鍍液中有金屬雜質(zhì) | a)假鍍 b)確認雜質(zhì)來源 c)更新鍍液 |
|
3)鍍液中含有機雜質(zhì) | a)更新鍍液 b)確認雜質(zhì)來源 |
|
4)鎳槽攪拌太弱 | a)增加攪拌及擺動速度 b)試出最佳攪拌條件 |
|
析出速度太慢 | 1)Ni槽溫度太低 | a)調(diào)整至正確溫度 |
2)Ni鍍液pH值太低 | a)用氨水調(diào)整pH值 b)檢查及調(diào)整控制器/補充裝置 |
|
3)Ni 槽金屬雜質(zhì)污染 | a)確認污染源 b)更新鍍液 |
|
4)Ni 槽有機雜質(zhì)污染 | a)更新鍍液 b)確認污染源 |
|
5)綠漆入Ni鍍液中 | a)更新鍍液 b)確認綠漆作業(yè)條件 |
|
鎳鍍液混濁 | 1)pH值太高 | a)用稀硫酸調(diào)整pH值 b)檢查及調(diào)整控制器/補充裝置 |
2)浴溫太高 | a)調(diào)整至正確溫度 | |
3)帶出量太多 | a)延長滴水時間 | |
4)藥液從管路泄漏 | a)管路修復 | |
析出保護裝置的電流太高 | 1)浴溫太高 | a)調(diào)整至正常溫度 |
2)pH值太高 | a)用稀硫酸調(diào)整pH值 b)檢查及調(diào)整控制器/補充裝置 |
|
3)局部過熱 | a)加熱器附近加強攪拌 b)使用熱交換器時,降低蒸汽壓 |
|
4)槽壁鈍化不良 | a)移出鍍液,使用硝酸鈍化 b)增加硝酸濃度或增加純化時間 |
|
析出保護裝置的電流太高 | 5)活化液帶入 | a)移出鍍液,使用硝酸浸漬 b)確認活化水洗槽進水量水洗時間 及水洗次數(shù) |
6)補充液流量太大 | a)檢查及調(diào)整控制器 b)檢查補充裝置 |
|
7)安定劑太低 | a)加強過濾 | |
8)掛架上的Ni/Au碎片掉入Ni槽內(nèi) | a)將掛架上的Ni剝除 | |
9)析出保護裝置異常 | a) 檢查線路及調(diào)整整流器 | |
Ni槽pH值起伏太大 | 1)前處理藥液帶入 | a)更新水洗水 b)確認水洗進水量及時間 |
2)帶出量太大 | a)延長滴水時間檢查管路是否泄漏 等 |
|
Ni消耗量太大或Ni濃度無法維持 | 1)帶出量太大 | a)增加補充時間 b)延長滴水時間 c)檢查管路是否泄漏等 |
2)鎳槽析出 | a)更槽 b)降溫移槽處理 |